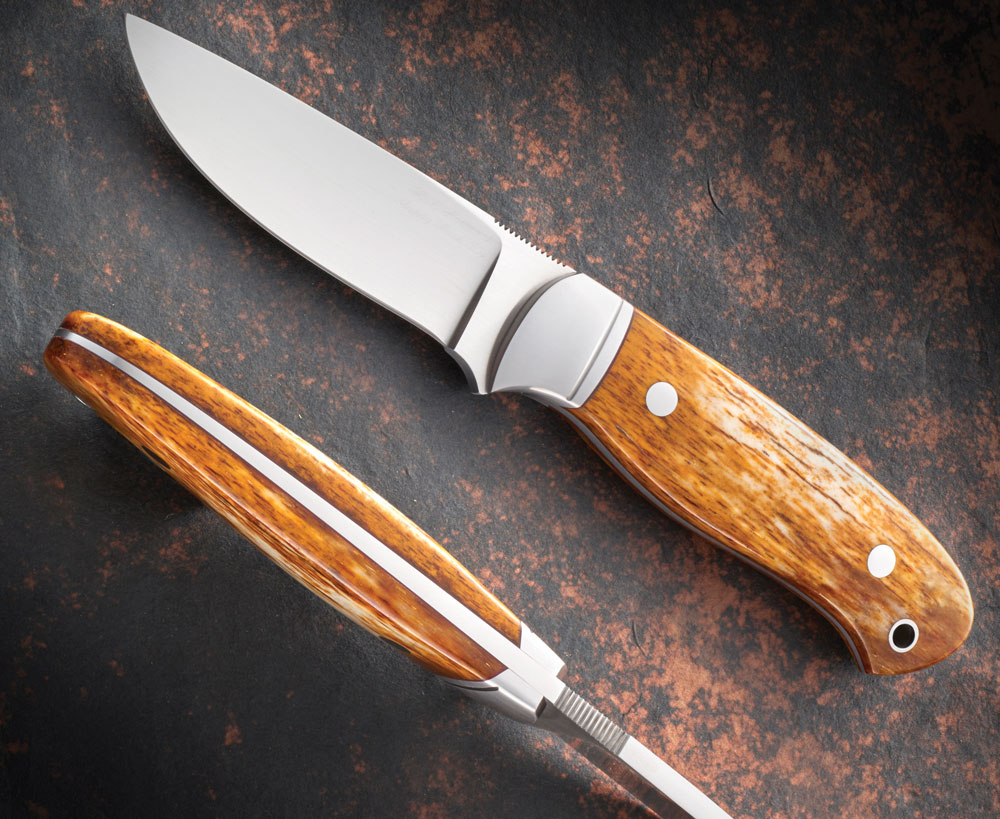
Bone handle knives are good to the bone, including some of the latest blades made today.
Bone is one of the earliest materials used on knife handles, becoming a high art during the early and mid-1800s when the factories in Solingen, Germany, and Sheffield, England, were peddling their wares to eager American consumers. When tariffs on the old-world manufacturers were imposed in the waning years of the 19th century, U.S. manufacturers gained a toehold on the domestic pocketknife market, and by the early 1900s were in high gear. Bone was the most prominent and popular handle material in those days—and remains among the most prevalent, if not the most prevalent, to this day.
Many offerings by pocketknife manufacturers are graced with bone scales, and custom knifemakers use it frequently on both fixed blades and folders. BLADE® went inside the knife industry to find out why bone remains such a dominant handle material on today’s knives.
Where’s the Bone?
Most bone used on knives is bovine—that is, from cattle. When you think about how much beef is consumed annually in this country, you have to believe there’s a whole lot of cow bone available. There is. We asked proprietor Joe Culpepper of Culpepper & Co.—a large wholesale supplier and processer of all types of handle materials to both factories and custom artisans—about the importance of bone on his bottom line.
“Cattle bone constitutes 98 percent of our total bone sales, with camel and giraffe being the remainder,” Joe says. “The overwhelming majority of the cattle bone that we use is from South America, although it is available in nearly every country that has a beef industry.
“We find that cutlers, both factory and custom alike, lean heavily toward browns, ambers, reds, oranges, blacks and other colors that are more conservative. This is probably a bit truer for the custom makers than manufacturers. As for surface texture, we sell a lot of the more traditional jigging patterns that resemble patterns used before World War II. Approximately 60 percent of our sales are to factories, custom knifemakers the other 40 percent.”
Joe indicates he has seen an increase in demand for bone in recent years and, along with it, an jump in prices.
“As with anything, costs are always rising. The cost of jigging, polishing and cutting bone is nearly always a product of labor costs, which is somewhat predictable. Coloring is a different story,” he notes. “All of the dye components have risen exponentially in recent years.
“As far as overhead goes, we have to buy the raw material, have it shipped to our processing plant, treat it, cut it into scales, bleach the scales, sort for characteristics, identify outliers, texture and jig the bone, stack it into vats, color with dye, and test and document a sample before we make the final product available to the industry. There are also hundreds of other smaller processes involved, but these are the major things.”
While jigged bone is the most popular, Joe has seen an uptick in stag or carved bone patterns made to simulate deer antler.
“Most of our varieties of our carved stag bone have seen a rapid increase in popularity in recent years,” he says. “This is primarily because of the ban and scarcity of genuine stag. To my knowledge, we made the first variety of carved stag bone in the 1980s. It was made based on a Delrin [a type of thermoplastic] sample. Carved stag bone is popular in a variety of colors including amber, green, and various shades of brown and orange.” While smooth bone is still popular, it lags behind the jigged and carved varieties—but it does have the advantage of being laser etched and scrimshawed.
A Case Study
“Bone handles have always given Case knives their distinctive look and feel,” begins Fred Feightner, Case marketing coordinator. “While all of our handle materials cycle from time to time in terms of consumer favoritism, bone remains our most popular. Right now we are using our traditional cattle bone, the same we’ve been using for generations. Beyond that, some of our synthetics, woods and shells, like mother-of-pearl and abalone, continue to be very popular.”
According to Fred, Case handles its own jigging and color-dying processes. “We receive the bone in smooth slab form, then do all of the work needed to turn it into beautiful Case knife handles—including jigging, dying, drying and cutting to size. There are costs implicit in our manufacturing plans as the bone is sometimes stored before it goes to the production floor. The slabs also need enough time to take just the right color shade before being moved to assembly operations.”
Feightner sees no let-up in the popularity of bone handles in the near future.
“Bone is such a traditional knife handle material. It remains among our top sellers at Case, which is probably true of most makers of traditional folding knives today. Even with all the new handle materials that continually enter the marketplace, there’s still something special about the way a bone handle completes the look of a Case knife. We see demand for traditional folders to continue to grow, especially for Case knives, as our distribution and reach continue to expand into new markets.”
Tried and True
Steve Koster is an American Bladesmith Society journeyman smith who specializes in traditional fixed blades, most featuring his exquisite handforged damascus as seen in the English-style bowie on page 37. It sports a forged 1084/15n20 feather-pattern damascus blade and a boxed-frame handle topped with thick jigged bone scales.
“I do not jig or dye any of my scales. I get most of them from various manufacturers and suppliers at knife shows,” he states. “The cheekbone scales on my English bowie came from Tru-Grit. I picked through the whole box to find a nice matched pair with a fine jigged pattern. Some of the jigged-bone patterns are not uniform so I have to spend time selecting a matched pair of scales to fit the tang or frame.”
Though Steve uses a wide variety of handle materials on his knives, bone finds its way onto a healthy percentage. “I do about two out of 10 knives with bone scales,” he says. “I like using natural handle materials, and bone has been used for knife handles for hundreds of years. It is very durable and I really like the look of anything natural or antique looking on handles. Natural cow bone, camel bone or any of the ancient bones can be used as they are, or can be stabilized.”
Koster opts for bone with a traditional look. “The imitation stag I don’t care for,” he notes. “I prefer bone that has been picked or jigged, and also bone sanded smooth with a natural finish.”
Rest Assured
The tactical end of the cutlery industry (page 12) has ruled the roost for many years—and with it synthetic handle materials such as Micarta®, G-10 and carbon fiber—but traditional knives (page 12) still garner a sizable segment of the market. If you’re one of those who appreciate old-school pocketknives and fixed blades, rest assured—the factories and custom knifemakers have your back!one is one of the earliest materials used on knife handles, becoming a high art during the early and mid-1800s when the factories in Solingen, Germany, and Sheffield, England, were peddling their wares to eager American consumers. When tariffs on the old-world manufacturers were imposed in the waning years of the 19th century, U.S. manufacturers gained a toehold on the domestic pocketknife market, and by the early 1900s were in high gear. Bone was the most prominent and popular handle material in those days—and remains among the most prevalent, if not the most prevalent, to this day.
Many offerings by pocketknife manufacturers are graced with bone scales, and custom knifemakers use it frequently on both fixed blades and folders. BLADE® went inside the knife industry to find out why bone remains such a dominant handle material on today’s knives.
NEXT STEP: Download Your Free KNIFE GUIDE Issue of BLADE Magazine
BLADE’s annual Knife Guide Issue features the newest knives and sharpeners, plus knife and axe reviews, knife sheaths, kit knives and a Knife Industry Directory.Get your FREE digital PDF instant download of the annual Knife Guide. No, really! We will email it to you right now when you subscribe to the BLADE email newsletter.
Click Here to Subscribe and get your free digital 2024 Knife Guide!