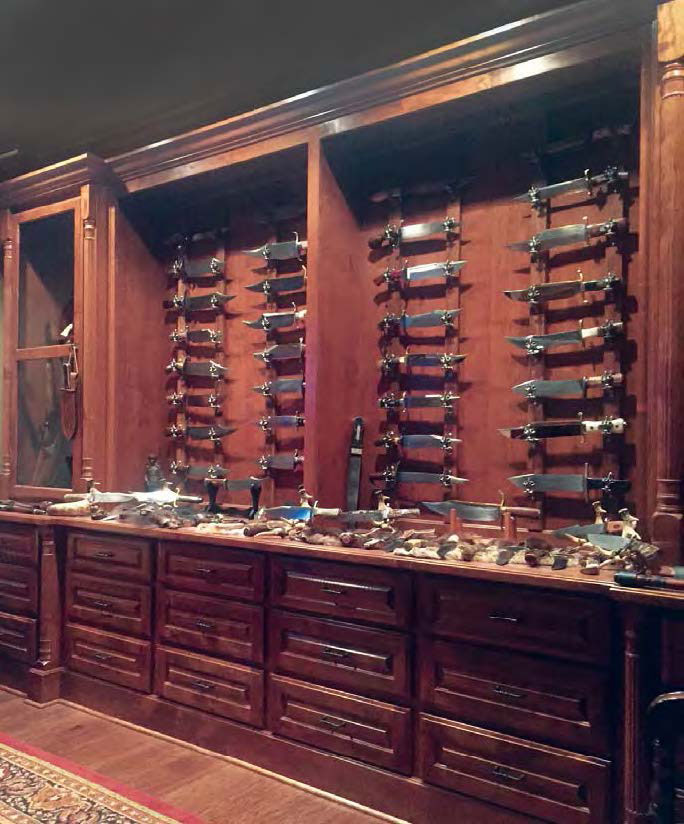
in his 7×14-foot display vault made of alderwood, including 18 drawers full of bowies at the
bottom. (All images by Chris Nolen unless otherwise noted)
Editor’s note: This article originally appeared in the February 2018 edition of BLADE. Download the issue here.
A Bowie Knife Collecting Obsession
The trail of the fabled bowie knife is long and winding. From the Sandbar Fight to the Alamo and beyond, its fact, mystery and myth have become the stuff of legend. The trail extends nearly 200 years, and for half his life Chris Nolen of West Monroe, Louisiana, has traveled down it.
For sure, he’s gone further than most.
At 65, Chris remains heavily engaged in a custom embroidery and screen print business called Reflections with his daughter, Lori Rockett, while another daughter, Lindsey Sanders, lives in Chattanooga, Tennessee. A retired telecommunications worker, he has sought and bought knives since his days mowing lawns for money so that he could run to the local hardware store and buy the knives that caught his eye.
“My mother still kids me about not having any money in those days because I was always buying knives,” he smiled.
Chris married his wife, Linda, 40 years ago, and shortly afterward his knife interest literally got bigger. He collected several large hunting knives by BLADE Magazine Cutlery Hall-Of-Fame© member Bo Randall and still owns a dozen of them, but he isn’t alone in the lure of the brawny bowie.
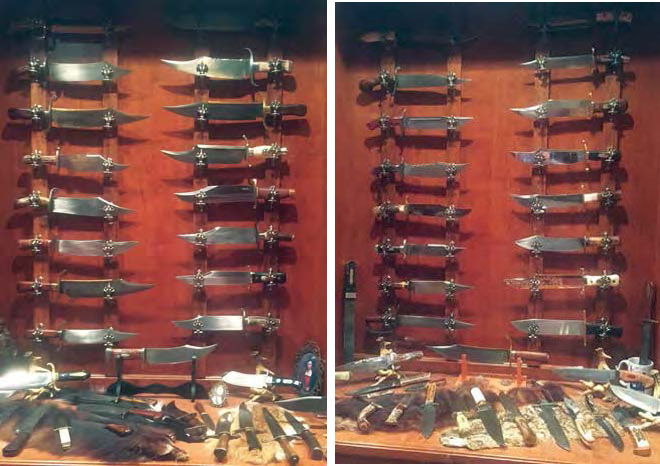
Cutlery Hall-Of-Famer Jim Bowie’s legendary encounter at the sandbar, his final hours at the Alamo, the association of numerous knives that bear his name with the history of Texas, its link to the Civil War, and its stretch across the Atlantic to beginnings in the cradle of quality knifemaking—Sheffield, England—made the bowie irresistible.
“It seems like every time I went to a show I was attracted to the big bowie knives,” he recalled. “Sometimes, you might say, ‘What are these good for?’ but I saw them as art in steel.”
Today, the Nolen collection of bowies tops 200, and a fortress-like display room keeps them safe and allows their owner to show them to visitors. One of Chris’s primary pursuits has been the history of the bowie along with a desire to own reproductions of some of the most significant bowies in history. He has worked with several top-notch custom knifemakers, pored over documents and traveled to various locations, the results of which are nothing short of spectacular.
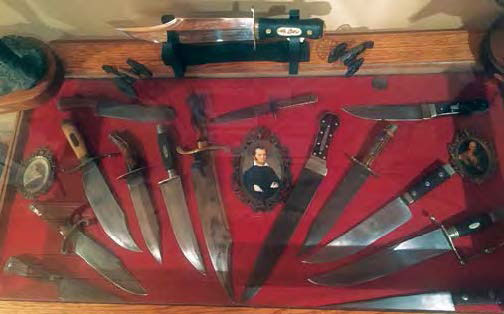
Among his bowies are repros of the Searles-Fowler bowie (the original of which is on display in the Alamo), the Joe Musso brass-back bowie, the Iron Mistress, the Jesse Clift bowie, the Juan Seguin Bowie and Bowie No. 1, to name a few.
“No Turning Back”
In 1986, Chris contacted knifemaker Jerry Berry of Natchitoches, Louisiana, after sketching a bowie. He asked if Berry could actually make the knife from the drawings. Of course, the answer was yes.
“That knife has a 9.5-inch blade with a slight recurve,” Nolen said, “with brass and nickel-silver trim and a solid stag handle with a hidden tang. The blade is ATS-34 stainless steel. That is one of my favorites because it was one of the first. Once I got it there was no turning back, and for the last 30 years I have pretty much stuck with the big bowies. Robert Blasingame of Kilgore, Texas, helped me get started on the making of copies of antique knives before he passed away in 2010. He was quite a historian.
Bringing Bowie Knife History to Life
“It was about 10 years ago that I got this wild idea to track back the bowie and its origin,” Chris continued, “and Linda and I visited 12 museums and met curators, who were all such nice people who even let us hold some of the original knives that were associated with the Bowie family.
“For example, we went to the Alamo and actually got the dimensions of the original Searles-Fowler knife. Now, we’ve researched and had reproductions made of pretty much every knife associated with the Bowie family.”
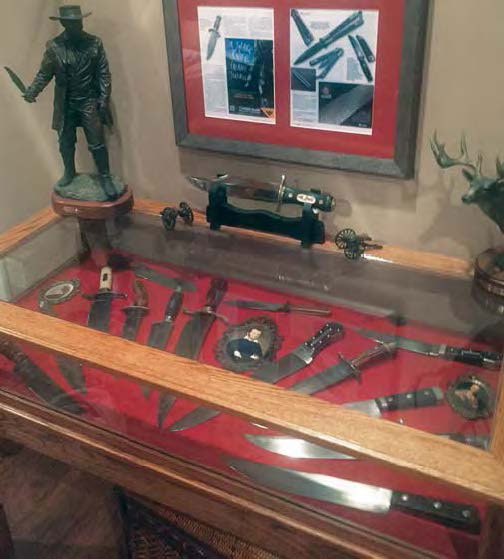
Through the years Chris has developed a reputation as something of an expert on bowie knives, resulting in his traveling exhibit aptly named, “Bowie Knife: Fact, Myth, and Legend.” In 2014, he traveled to the Historic Arkansas Museum in Little Rock, where more than 200 genuine bowies were on display.
“They had my reproductions at the entrance there in a big black case,” he remembered. “There is probably more legend than anything surrounding these knives. Jim Bowie didn’t leave us much to go on, and I have studied him for years now. His brother, Rezin, was a big promoter of the bowie knife and gave a lot of them away as gifts. These reproduction knives have been everywhere, and I get a kick out of it.”
Along with the history lesson that the bowie repros convey, visitors can begin to grasp the tremendous skill that is required to produce a high quality bowie.
“It’s hard for a maker in today’s time to get into the head of a maker from 180 or 200 years ago,” Chris offered, “and most of them want to put their own artistic spin on a knife. But along with Jerry Berry, I narrowed it down to Rich McDonald and Mark Banfield who do a lot of work for me, and Cowboy Bob Giles of Whitefish, Montana, who has probably made 15 of them for me. These men are unbelievable artists.”
Musso and Musician Phil Collins
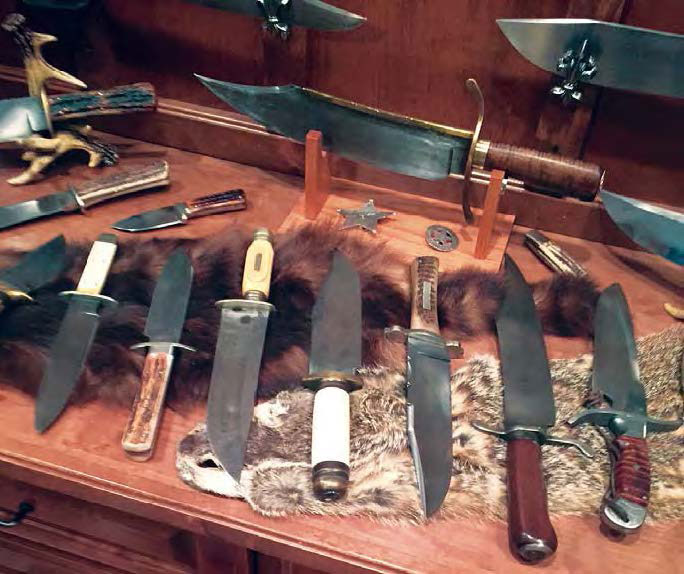
Mention of the Musso Bowie conjures some of the theory and conjecture surrounding its authenticity.
According to Chris, Joe Musso sold the original knife to Phil Collins of the rock music group, Genesis, who in turn donated the original to the Alamo, where some metallurgical testing has been done and some believe the “JB” mark on the guard ties the knife to Jim Bowie.
“That is one of my favorite reproductions because Mark [Banfield] went the extra mile and even copied the stains on the blade,” Chris commented, “and it is the only authorized true copy of the Musso knife. I have some Samuel Bell copies and one of my favorites was just done by Giles. It is an exact copy of the Charles Congreve knife done in Sheffield around 1835, a big swayback bowie trimmed in silver.”
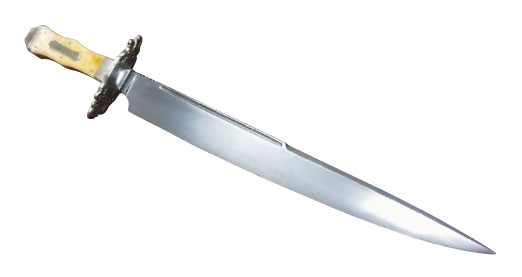
A “Dazzling Display” of Bowie Knives
A couple of years ago Chris and Linda decided to build their dream house on a tract of land they had owned for a while. The move brought to light several knives that had been packed away for 20 years or so. Thinking about the future of his collection, Chris decided to make space available to display it properly.
“I always wanted to have a secured room to display the knives in,” he remarked, “so we designed this room 20 by 18 with no windows, solid brick, and with concrete next to the brick. It would take a tank to get into this thing. There is also a solid steel security door, so it is pretty much a vault. Lori’s husband, Marc, owns a custom cabinet shop. He cuts wood with a laser, and he cut out an entire wall and put in a cabinet for guns to go on each end and 18 drawers at the bottom. You can pull out the knife displays. There are two center panels, and the display is 14 feet wide and 7 feet tall. The center panels have 32 pewter hangers in a fleur-de-lis design that hold 32 bowie knives. At the bottom is a 3-foot shelf that holds about 40 bowies.
“It isn’t everywhere that you can see 70 or 80 bowie knives in the open,” Chris added. “People come in and they have to catch their breath. I also have a coffee table with a glass-top display that holds about 20 knives and is kind of my dedication to Davy Crockett. The other side of the room is a glass display of the ‘Fact, Myth, and Legend.’ The cabinetry is all of alderwood.”
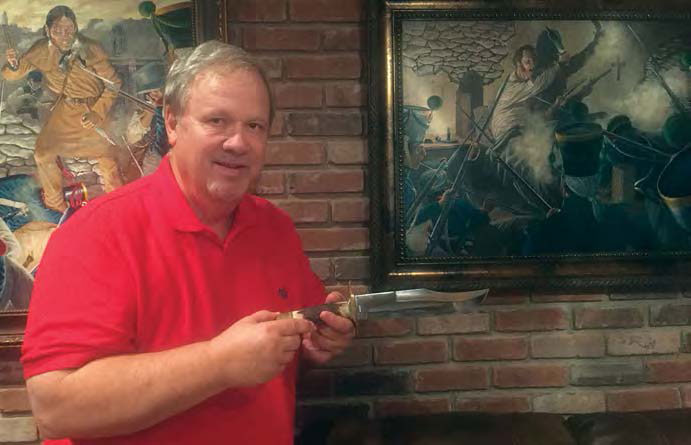
To complete the dazzling display, Nolen commissioned three paintings depicting the epic of the bowie knife during the desperate, heroic stand at the Alamo. The first painting depicts the death of Jim Bowie, slashing defiantly at Mexican soldiers from his cot.
The second depicts the death of Crockett, a death which is surrounded in controversy. The artist allows the viewer to decide Crockett’s fate, depicting the legendary Tennessee long hunter and adventurer standing but exhausted.
The third depicts the death of Col. William Travis, commander of the doomed Alamo garrison.
Although it might seem to the casual observer that the Nolen journey down the bowie trail is complete, such is not the case.
Chris continues to add to his collection. Mark Zalesky, editor of KNIFE magazine, recently pitched in to assist with the recreation of a Samuel Bell knife located in Knoxville, Tennessee, and Mark Banfield completed the addition.
The road goes on forever.
Make Your Own Knives
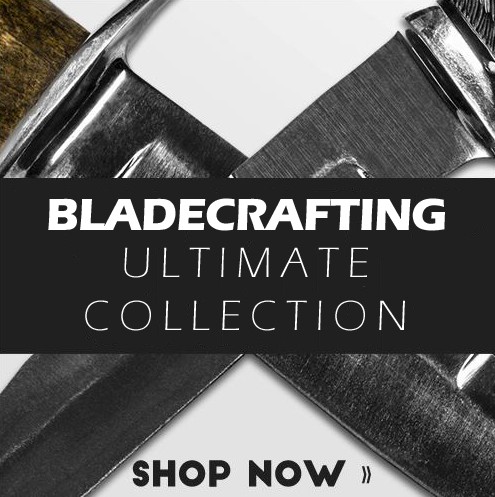
Bowie knives are one of the first projects new knifemakers undertake. Get started with this collection of hand-picked books from BLADE.