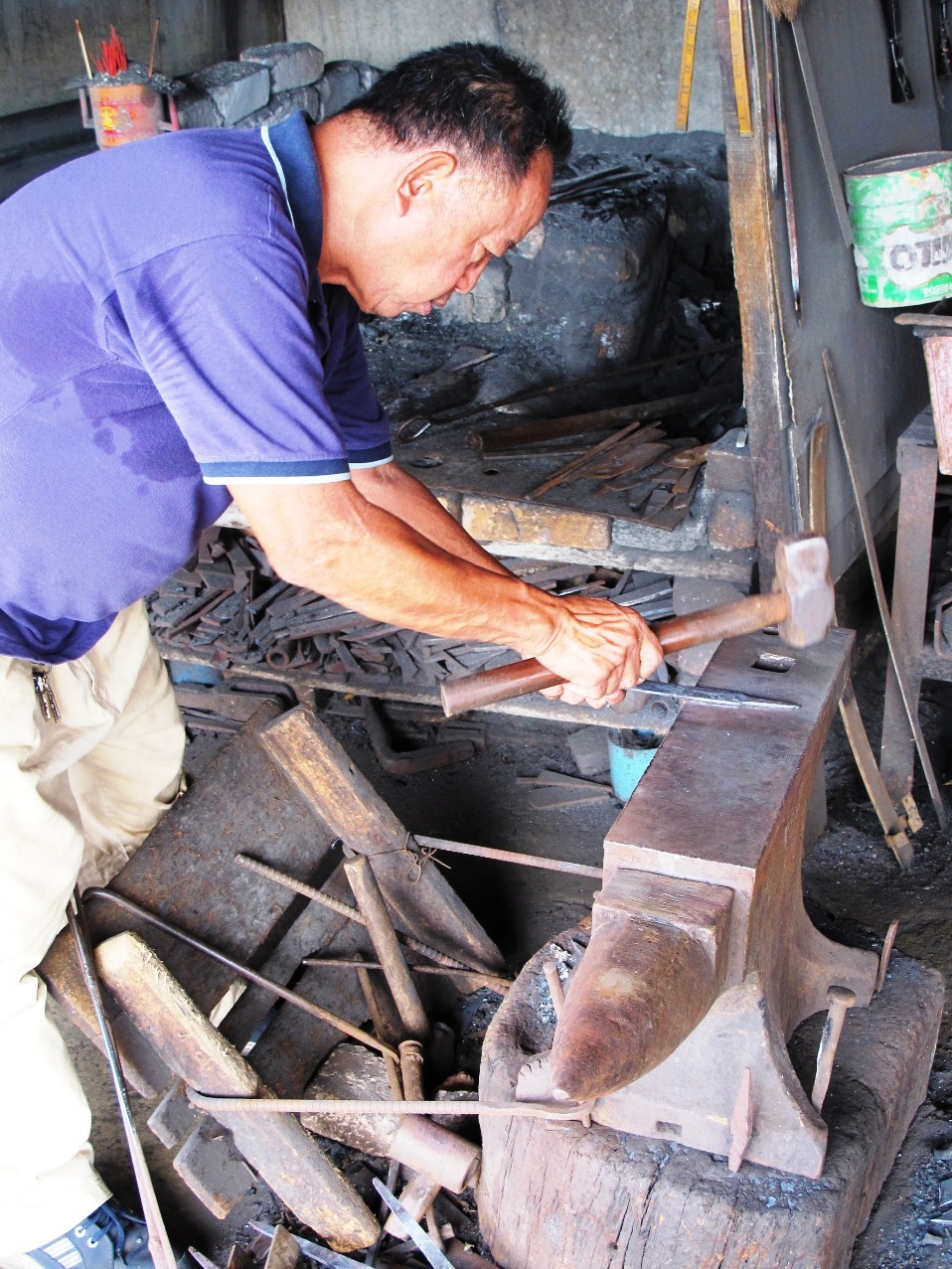
Lim Loong Hoi hammers steel in his old school knife shop in Selangor, Malaysia. (photo courtesy of Philip Lim Chin Guan)
Every morning, Lim Loong Hoi is at his dirty workshop—it looks more like a shack from the front—at about 8 o’clock. Beyond the open door in the rear, the passage leads to a hallway and a few small rooms.
The boneshaker of a wooden shop has been home to Lim and his family for decades. He said he has been making utility tools, including parangs, goloks, large fisherman’s blades and sickles, since his school days.
His instructor and mentor was his grandfather. Back in the day, Lim found time after school to help his grandpa at the workshop. Picture a teenager’s delicate hands with a heavy hammer and a pair of tongs when, during morning hours, he was holding a pen or ruler in school. That was about 50 years ago.
Called Sin Sam Hup Lee, Lim’s shop still stands firm against fluctuating economic conditions and the ravages of time. His back is slightly bent from the long, dreary years of standing before the furnace or hydraulic pump, pounding away at pieces of elongated steel.
Pasir Penambang is a small village on the outskirts of Kuala Selangor in the state of Selangor, Malaysia. The locals, especially the Chinese, are mostly fishermen, shopkeepers or fish wholesalers.
The Chinese fishermen are Lim’s regular customers. The edged tools he makes for them are larger than usual. The blades are similar to huge butcher knives, having a curvature that helps in slicing a big fish in two with one swift, downward stroke.
The Malay farmers usually ask for long sickle blades used in dislodging oil palm fruits, a.k.a. kelapa sawit nuts. Each sickle is hollowed out at the handle to accept a long pole. The pole enables the user to extend the blade about 7 to 8 feet to harvest the nuts from the palm trees. Each sickle costs $2 to $2.60. The price depends on the quality of the steel and blade size.
In Lim’s workshop, stacks of Jeep leaf springs used for blade steel rest in a corner. The four-wheel-drive springs are rusty and grimy. The haggard bladesmith likely sourced the spring steel pieces by the ton from an old junkyard. He probably got them cheap, too. Most of the time they are cut to required lengths. It is a low-tech, slightly primitive method of stock removal.
Practicality and function rule the land. Almost nobody here has heard of CPM-S30V, VG-10 or ZDP-189. The most convincing line Lim uses is, “This is Jeep spring steel.” That alone gives his customers some assurance they are getting quality steel.
Edged tools used by fishermen or farmers in the fields have no time to get rusty because they are used regularly and on a daily basis. After six to eight years, the parang, golok, fisherman’s blade or farmer’s sickle may be deemed unusable. The user simply buys another one from Lim. After all, it costs just a few bucks. Compared to its long-term usefulness and hardiness, the cost per blade is minuscule—which is why the agrarian folk in Pasir Penambang and nearby villages are Lim’s loyal customers.
Lim’s assistant is taciturn, works like a well-oiled machine and knows the blade-making process intimately. Like his boss, the assistant relishes the feel of steel in his hands.
Of course, the untidy workplace is not exactly ideal for a private conversation. Customers determine what they want, haggle over the price and depart with the edged tool they bought wrapped in a newspaper.
Occasionally, some outsider brings a drawing of the piece he wants made. The bladesmith examines the drawing and then determines whether his outdated equipment and other machines are suitable for the order.
The volume of edged tools he sells will not even make Lim a member of the middle class. He obviously is not making a fortune, as some people may suspect.
Ah Pee
A couple of doors away along the same row of wooden shops is another knifemaker, Ah Pee. A sign at the front of his establishment says “Chuan Lee Chan.” Originally from China, he has aged before his time, though his eyes have a certain fire that belies his years.
Pee said his children, especially his son, have absolutely no interest in knifemaking. “The young men today prefer air-conditioned offices and as little dirt on their hands as possible,” he told me.
The long hours and intense heat from the furnace are enough to deter most from pursuing such a profession. It is backbreaking work with the added disadvantage of low and slow financial returns.
After about five decades of using the hammer, tongs and grinder, Pee is long past set in his ways. He probably does not know how to do anything else. Perhaps he feels he is too old to learn and master another profession.
Not all the edged tools sold at both shops are fashioned by the resident makers. They also stock production parangs and some made-in-China models, both more affordable than the handmade models. Lim’s and Pee’s knives cost more because they factor in labor, time and the type of spring steel used. The sharpness of the blade is guaranteed.
Sometimes each bladesmith will ask the customers how the parangs or knives will be used. Then he might recommend another type of edged tool. The heavy-duty blades—those for chopping hardwood, the bones of livestock, etc.—are made to different specifications than those for skinning and other light work. The smiths’ skills with iron and steel are invaluable to those who need their tools to make a living.
Heat Treating and Sharpening
Heat treatment consists of quenching the steel in a trough of water. There is no set formula for giving a hardened edge. Pee said it all comes down to “feel.” The long years of experimenting with quenching a red-hot blade in water have given him the intuition and the right recipe of crucial seconds of sinking a piece of hot steel into a trough, and then lifting it up at just the right moment. I have seen Pee do it on several occasions. He said without the special “water treatment” the blade would not hold an edge.
Sharpening a parang or any kind of blade is done on a hand-held metal grinder. The way Pee does it looks easy—until you put the same grinder in your hands. A flat grind is apparently the way to go.
First, he clamps the blade on a table vise, covers his mouth with a piece of cloth and dons plastic goggles. He moves the grinder side to side and applies just the right amount of pressure.
A shower of bright orange sparks fly past his body but Pee pays them no heed. When he is fully satisfied the blade has the correct grind, he unclamps it and adds the finishing touches to the edge with a smooth stone.
Again, it is all “touch and feel.” When a man has spent three-quarters of his life sharpening blades, you do not question his judgment. He said, “The blade can easily shave the hair on the arm.” I believe him totally.
He then gives me a piece of invaluable advice. After the blade has been used, wash it in running water. Do not wipe the water off but put the knife out in the sun to dry. Allow the sun to dry the steel blade and it will remain sharp indefinitely.
It took awhile before I realized the wisdom of his words. The tropical weather, coupled with the scorching Malaysian sun, acts as a form of heat treatment on the sharpened blade. Perhaps the sun’s rays strengthen the already hardened molecular structure of the blade’s edge? Who knows better—the bladesmiths of Pasir Penambang or me, the end user from the city?
Paying Homage
There are only two bladesmiths along the main road in Pasir Penambang. Both are advancing in age. This is a dying trade. The youngsters are not interested. Those of us who appreciate all things steel and sharpened tools come to this tiny town, away from the hustle and bustle of the bigger cities, to pay homage to men of steel who live a life of quiet desperation.—By Philip Lim Chin Guan
To read similar stories and all about the latest knives, knifemakers, knife trends and much more, subscribe to BLADE®. For more information click on http://www.shopblade.com/product/blade-magazine-one-year-subscription-us/?r+ssfb141211#BL1SU